T800/T1000 Carbon Gravel Wheelsets
Explore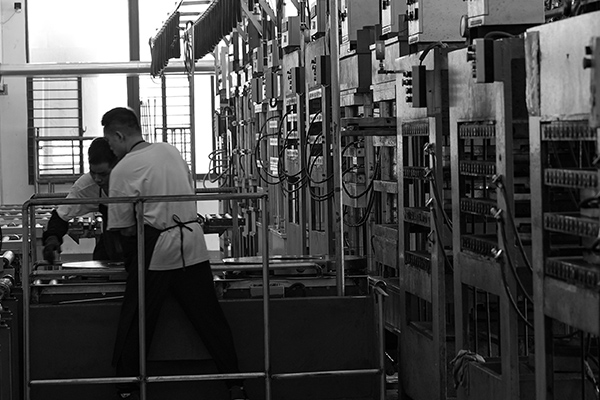
Core Services
From design to delivery, we're your complete carbon gravel wheels solution:
30+ Rim Profiles
Comprehensive rim design and manufacturing capabilities covering all gravel disciplines. Available rim depths: 35/40/45/50mm with internal widths of 21/23/25mm for optimal gravel tire support (35-50mm tires). Custom mold development completed in 45-60 days including full FEA structural analysis for rock impact resistance, CFD simulation for crosswind stability, and wind tunnel validation at 20-40km/h speeds typical in gravel racing. Each profile undergoes 3-month field testing across varied terrain including hardpack, loose gravel, and rocky sections. Design features include 4.5mm hookless bead walls for pinch flat protection, reinforced spoke beds for high-tension gravel builds (130kgf), and terrain-specific carbon layup schedules optimized for vibration damping. All molds manufactured using 5-axis CNC technology with ±0.02mm tolerance control for consistent tire seating and tubeless performance.
Read More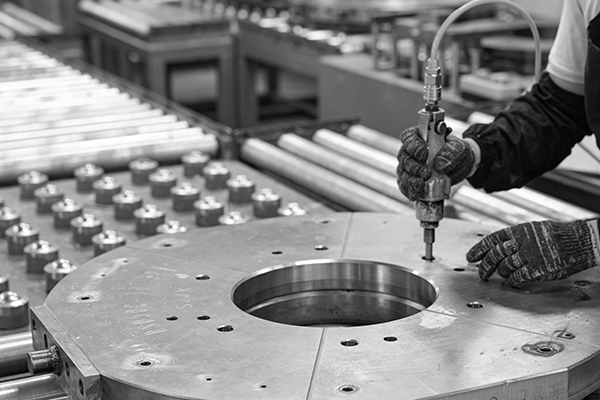
10-200 Set Batches
Streamlined production process optimized for medium-volume gravel wheelset manufacturing (10-200 sets) with 30-45 day delivery timeline. Each production run includes comprehensive documentation: ISO 9001 material certification for T800/T1000 carbon fiber, EN14781 impact test reports simulating rock strikes, individual spoke tension measurements (120-130kgf) for rough terrain stability, and detailed QC records. Manufacturing process features automated prepreg cutting with terrain-specific fiber orientations, CNC-controlled layup templates for consistent impact resistance, precision bladder molding (6-bar pressure/130°C cure) for optimal compaction in reinforced areas, and computerized resin content analysis ensuring durability in wet conditions. Production line maintains Class 10000 cleanroom standards for critical layup operations, essential for achieving void-free construction in impact-prone areas.
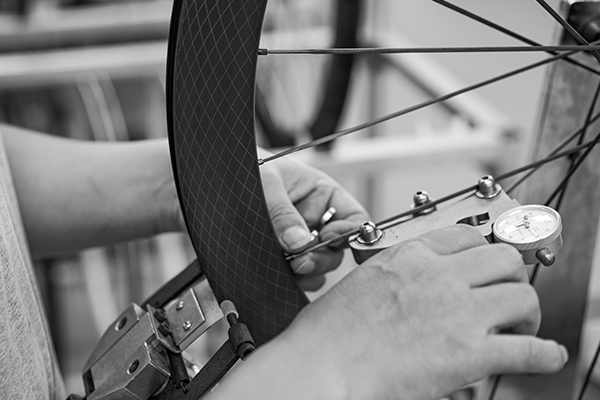
5-Stage QC Protocol
Comprehensive quality control system exceeding UCI gravel racing and ISO 4210 requirements. Stage 1: Impact resistance testing (1200J threshold) simulating rock strikes at 25km/h with high-speed camera analysis of rim deformation. Stage 2: Automated spoke tension measurement (120-130kgf) with electronic mapping for wheel stability on rough terrain. Stage 3: Tubeless compatibility verification including 6-bar pressure testing for 24 hours and dynamic air loss measurement (<0.5 bar/24hr) during simulated gravel impacts. Stage 4: Precision trueness verification (lateral/radial runout max 0.2mm) for consistent handling in technical sections. Stage 5: Surface finish inspection including mud-release coating verification, impact resistance testing at -20°C to +50°C, and UV stability testing (500-hour exposure) for all-weather durability. Additional testing includes loaded bikepacking simulation (100,000 cycles at 120% rated load).
Our Most Popular Products
Explore our wide range of categories and find the perfect product for you, from the latest fashion trends to the best deals on electronics.
Our Manufacturing Process
Professional carbon gravel wheelset manufacturing process from specification to delivery. Each step is optimized for gravel-specific performance requirements:
Technical Consultation
Detailed discussion of your gravel riding requirements including: terrain types (hardpack/loose/rocky), typical tire widths (35-50mm), expected loading (race/bikepacking), and local weather conditions. Our engineers provide rim profile recommendations (35-50mm depth) and internal width options (21-25mm) based on your specific use case.
Specification Development
Engineering team develops complete technical package including: carbon fiber selection (T800/T1000), layup schedule optimization for impact resistance, spoke count configuration (24/28/32H), hub selection (54T-690T engagement), and surface treatment specifications for local conditions. Full documentation provided with FEA analysis results.
Prototype Validation
Production of validation wheelset with full testing protocol: impact resistance verification (1200J), spoke tension optimization (120-130kgf), tubeless compatibility testing (6-bar), and field testing on representative terrain. Includes comprehensive test report and high-speed camera analysis of impact performance.
Production Engineering
Implementation of gravel-specific manufacturing processes: CNC-controlled fiber orientation, precision bladder molding (130°C cure), automated spoke tensioning to terrain-specific values, and Class 10000 cleanroom layup environment. Real-time quality monitoring with computerized process control.
Quality Verification
Five-stage quality control protocol including: structural integrity verification (EN14781/ISO 4210), electronic spoke tension mapping, dynamic tubeless air retention testing, digital trueness measurement (0.2mm tolerance), and surface finish inspection including mud-release coating verification.
Delivery Preparation
Professional wheel preparation including: tubeless tape installation, valve stem fitment, QC documentation package, and specialized packaging designed for international shipping. Each wheelset undergoes final inspection including bearing smoothness check and freehub engagement verification.
Manufacturing Process
Our standardized manufacturing process ensures consistent quality for every wheelset
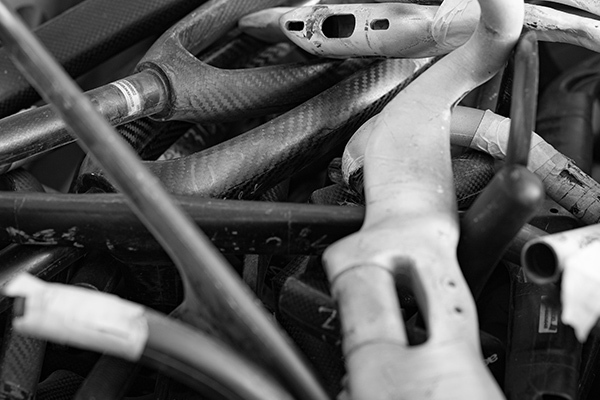
Material Inspection
All incoming materials including carbon fiber prepreg, resin, and hubs undergo strict quality inspection. Each batch of materials is documented with detailed inspection records and certificates to ensure production standards are met.
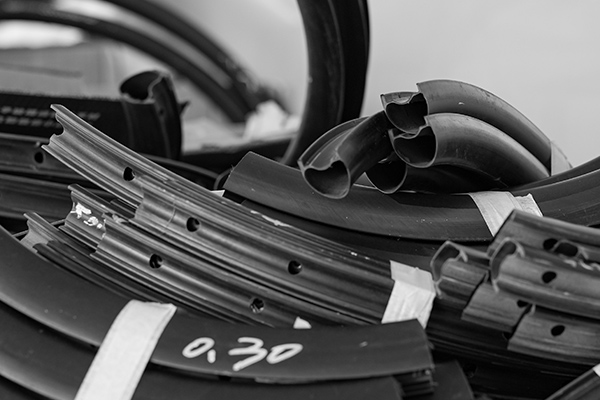
Manufacturing
Using proven molding techniques, our skilled technicians follow strict manufacturing procedures. Each step has detailed operation guidelines and quality control checkpoints to maintain product quality.
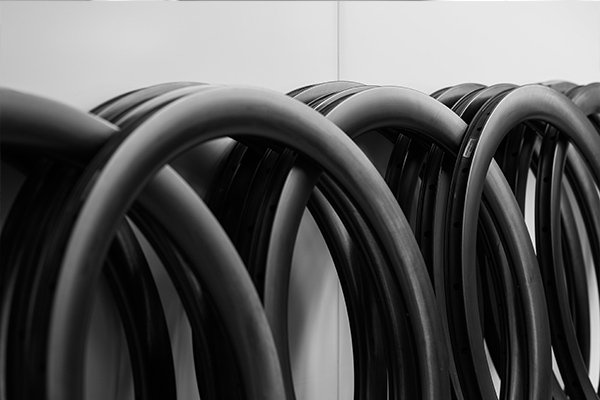
Final Inspection
Each wheelset undergoes comprehensive testing before shipment, including dimensional measurement, visual inspection, and performance testing. Every product includes quality certification documentation.
Workshop Environment
Our facility maintains professional standards for carbon wheel manufacturing
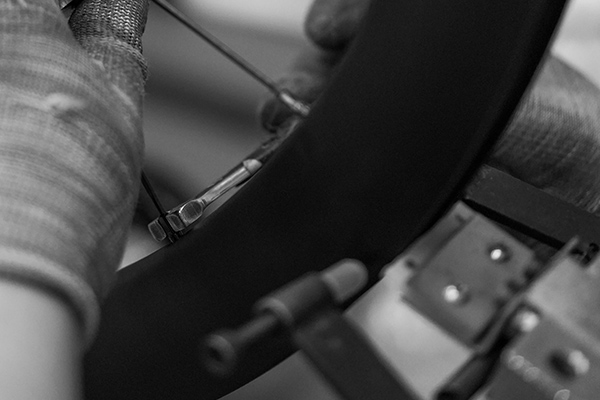
Material Storage
Temperature-controlled storage area for carbon fiber materials and resins, maintaining optimal conditions for material stability and quality.
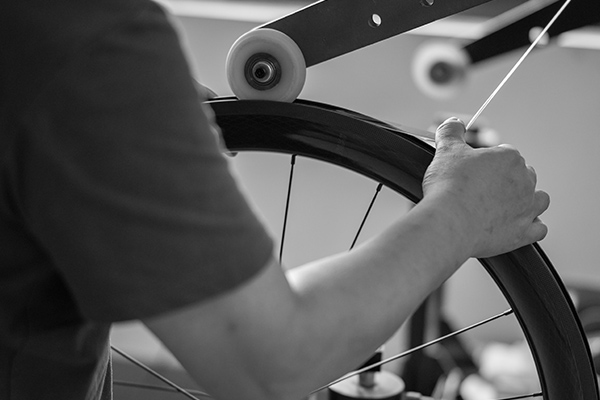
Production Area
Clean and organized production floor with dedicated stations for layup, molding, and wheel building processes.
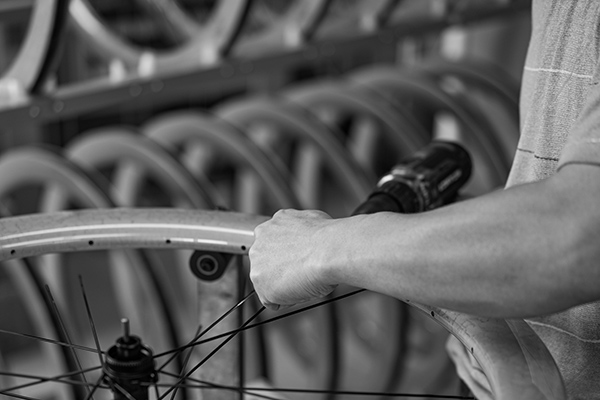
Quality Control
Dedicated testing area equipped with precision instruments for dimensional checking and quality verification.
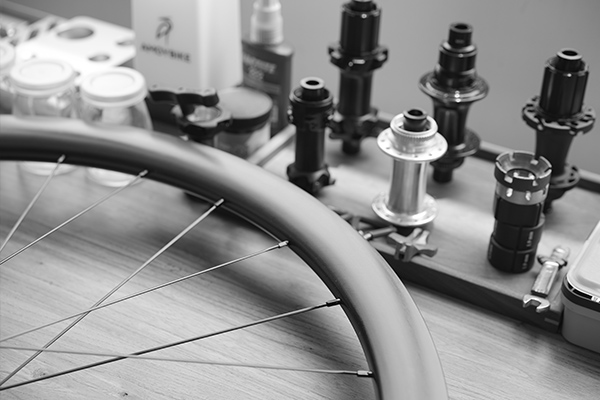
Assembly Line
Professional wheel building stations with proper tools and equipment for consistent wheel assembly and truing.
Manufacturing Capabilities
Our production line is equipped to handle both small and medium-sized orders efficiently
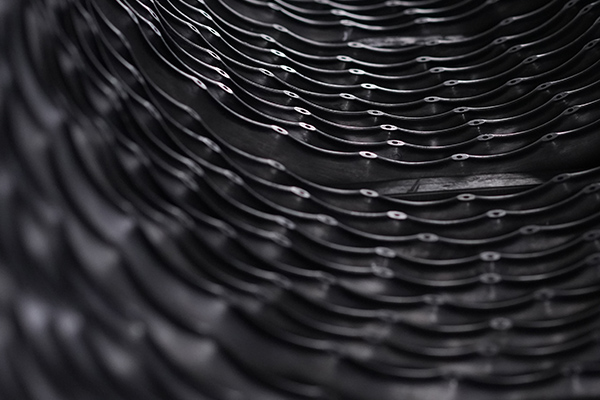
Carbon Layup
Professional carbon fiber layup process with experienced technicians ensuring proper fiber orientation and compaction for optimal wheel strength.
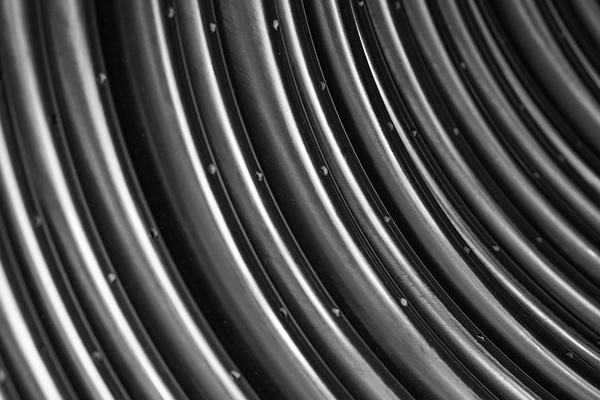
Molding Process
Temperature-controlled molding system with precise pressure control for consistent rim production. Each mold undergoes regular maintenance for quality assurance.
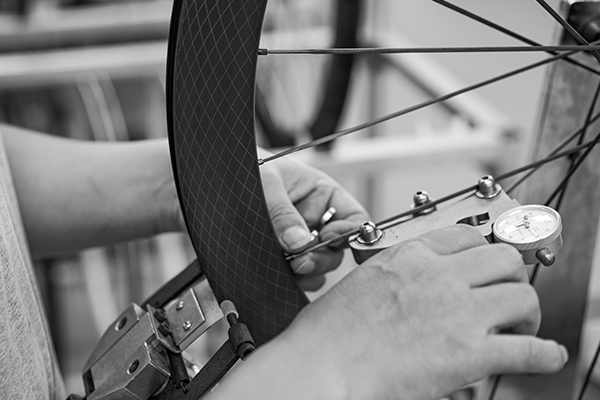
Wheel Building
Professional wheel building station equipped with tension meters and truing stands. Each wheel is built to specification by experienced wheel builders.
Why Choose Our Carbon Gravel Wheels
We create premium Carbon Gravel Wheels that deliver exceptional performance and reliability. Our professional-grade carbon gravel wheels are trusted by cyclists and teams worldwide for their superior quality and consistent performance.
Gravel-Tested Technology
Our facility uses cutting-edge carbon fiber technology to create wheels that withstand the demands of mixed-terrain riding. Each wheelset features T800/T1000 carbon construction, precision-engineered hookless beads (4.5mm wall height), and impact-resistant layup schedules tested to 1200J. Our proprietary molding process ensures void content below 0.5% for maximum durability.
Ride-Specific Customization
Our engineering team develops terrain-specific wheel configurations based on your riding demands. Choose from 35-50mm rim depths, 21-25mm internal widths, and specialized spoke patterns (24/28/32H). Hub options include high-engagement systems (54T-690T) for technical terrain, with ceramic bearing upgrades available for reduced rolling resistance.
Expert Gravel Assistance
Our technical team provides comprehensive support including terrain analysis, tire compatibility recommendations (35-50mm), and pressure optimization (25-45psi). We offer detailed setup guides for tubeless installation and maintenance schedules based on riding conditions. Post-sale support includes spoke tension verification and trueness adjustment services.
Terrain-Optimized Engineering
Each rim profile undergoes FEA impact analysis, CFD simulation for crosswind stability (20-40km/h), and wind tunnel validation. Our designs feature asymmetric rim profiles for optimal spoke tension balance, reinforced spoke beds (130kgf capacity), and terrain-specific carbon layup schedules validated through 100,000-cycle fatigue testing.
Comprehensive Gravel Range
Select from UCI-certified rim profiles optimized for specific terrain: 35mm (technical), 40mm (all-round), 45/50mm (race). Available with multiple hub configurations, spoke counts tailored to rider weight and usage, and surface treatments including mud-release coatings and UV-resistant finishes tested to 500 hours exposure.
Rapid Gravel-to-Race Production
Streamlined manufacturing with 30-45 day delivery for custom orders (10-200 sets). Production includes automated prepreg cutting (±0.5mm accuracy), CNC-controlled layup, and precision bladder molding (6-bar/130°C). Each batch undergoes real-time quality monitoring in our Class 10000 cleanroom facility.
Gravel-Ready Quality
Five-stage QC protocol including impact resistance verification (EN14781), spoke tension mapping (120-130kgf), tubeless compatibility testing (6-bar/24hr), digital trueness measurement (0.2mm tolerance), and surface finish inspection. Additional testing includes loaded bikepacking simulation and thermal stability verification (-20°C to +50°C).
Global Gravel Access
Professional wheel preparation including tubeless tape installation, valve stem fitment, and comprehensive QC documentation. Specialized packaging designed for international shipping with bearing protection and axle end caps secured. Each shipment includes detailed setup instructions and maintenance guidelines.
Our Story
Since 2008, we've been at the forefront of carbon wheel technology for gravel riding, earning trust from cyclists and teams worldwide. Our manufacturing process combines advanced carbon fiber expertise with rigorous quality control at every step. We've established ourselves as industry leaders in carbon gravel wheel innovation and manufacturing excellence.
About Us
Since 2008, we've been at the forefront of carbon wheel technology, earning trust from cyclists and teams worldwide.
Our manufacturing process combines advanced carbon fiber expertise with rigorous quality control at every step.
We've established ourselves as industry leaders in carbon wheel innovation and manufacturing excellence.
Customer-centric approach with 24/7 support.
Industry-leading product quality and innovation.
Sustainable and eco-friendly practices.
Comprehensive after-sales service.
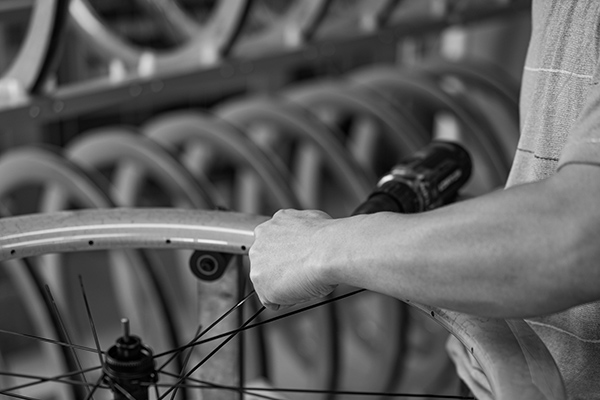
Frequently Asked Questions About Our Carbon Gravel Wheels
Find answers to common questions about our Carbon Gravel Wheels, manufacturing process, and services.
Return Policy
Product Information
Customer Support
Customer Reviews
Hear what our customers say about their experience with our carbon wheels.
These gravel wheels handle everything from smooth hardpack to chunky rock gardens. The 25mm internal width gives excellent tire support, and they've stayed true even after my roughest adventures. Perfect balance of durability and speed.
John Stevens
Gravel Race Champion
Our shop has built countless wheelsets for gravel bikes. These wheels offer exceptional value - the hookless design makes tubeless setup a breeze, and customers love the wide range of customization options for their specific gravel riding needs.
Mike Roberts
Gravel Bike Shop Owner
I needed tough wheels for loaded bikepacking that could still feel fast on smoother sections. The custom layup schedule they recommended is perfect - stiff enough for climbing but compliant on rough terrain. 2000 miles in and still going strong!
Sarah Thompson
Gravel Bikepacking Enthusiast
Our Location
5F, Bldg 3# Lianxing Tech. Park, NO. 32 Xinyuan Road, Xiamen, China, 351022
Call Us
+86 592 5620028
Get in Touch
Working Hours
Monday - Friday: 9:00 - 18:00